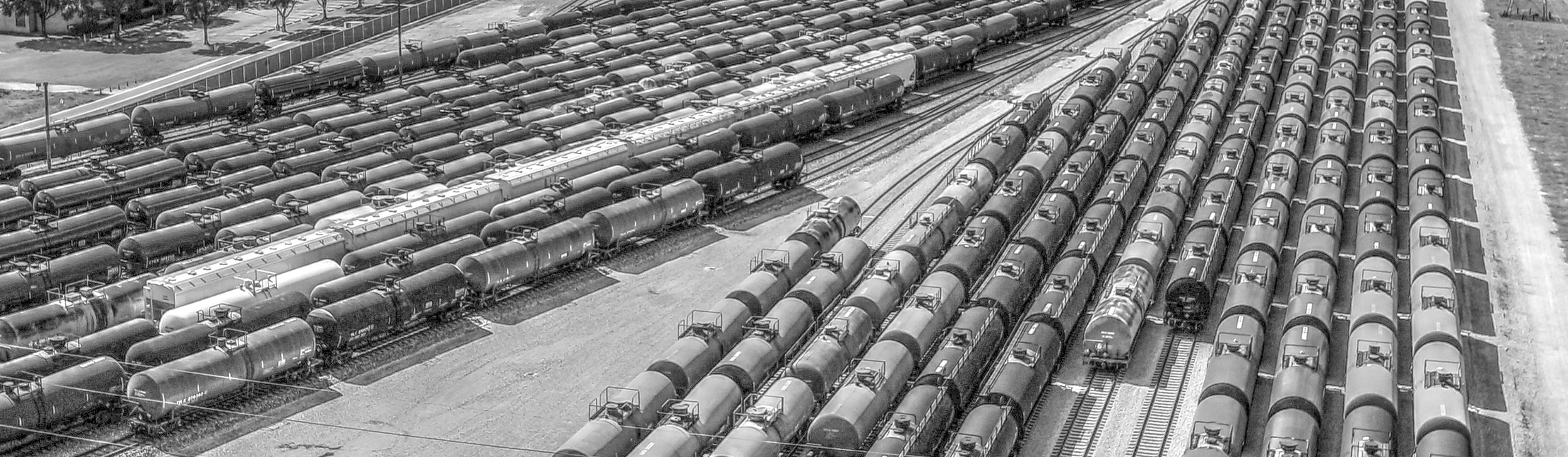
TRANSLOADING LNG TO RAILCARS
Transloading LNG (liquefied natural gas) to railcars involves the transfer of LNG from one mode of transportation or storage, such as trucks, pipelines, or liquefaction facilities, to railcars specifically designed for cryogenic liquids. This process enables LNG to be efficiently moved from production sites to distant markets where pipeline infrastructure is limited or unavailable. Here’s an overview of the transloading process, equipment, safety considerations, and benefits:
1. Overview of LNG Railcar Transloading Process
- Loading Stations: LNG is typically transloaded to railcars at dedicated facilities equipped to handle cryogenic temperatures and large volumes of LNG. These transloading stations are often located near liquefaction facilities, LNG storage hubs, or ports.
- Cryogenic Transfer Equipment: To transfer LNG, specialized cryogenic pumps, hoses, and connectors are used to maintain the LNG at extremely low temperatures (-160°C or -260°F) and prevent vaporization. The equipment must be capable of handling LNG’s properties and maintaining its temperature to avoid gasification during loading.
- Railcar Types: Railcars used for LNG are specially designed cryogenic tank cars that are double-walled and vacuum-insulated to minimize heat transfer and maintain the LNG in a liquid state. These railcars are designed to meet strict safety and performance standards for handling LNG.
ADVERTISEMENT
2. Equipment Used in LNG Transloading
- Cryogenic Pumps: These are used to pump LNG from storage tanks into railcars. They are specially designed to operate at low temperatures and maintain the pressure required for loading.
- Insulated Hoses and Couplings: LNG hoses and couplings are cryogenically insulated and must have safety features to prevent leaks. They are also fitted with quick-connect couplings for efficient transfer and emergency shutdown systems.
- Pressure Management Systems: LNG expands as it warms, so pressure control systems are essential during transloading to ensure that railcars do not exceed safe pressure limits. These systems also help vent any boil-off gas safely.
- Vapor Recovery Systems: Boil-off gas (BOG), which results from LNG warming during transfer, must be safely managed. Vapor recovery systems capture BOG and direct it to storage or reinject it into the tank to prevent loss and reduce emissions.
3. Safety and Regulatory Considerations
- Temperature and Pressure Monitoring: Constant monitoring is essential to ensure that the LNG remains in a stable liquid state and that pressure does not exceed safe limits during transfer. Any deviations trigger safety protocols to avoid accidents.
- Emergency Shut-Off Systems: Transloading facilities are equipped with automated emergency shut-off systems to halt the transfer in case of a leak or equipment malfunction.
- Personal Protective Equipment (PPE): Personnel involved in LNG transloading wear specialized PPE, including insulated gloves, face shields, and full-body protection to shield against extreme cold and possible gas exposure.
- Regulatory Compliance: LNG transloading operations are subject to strict regulatory oversight. In the U.S., for instance, the Department of Transportation (DOT) and the Federal Railroad Administration (FRA) set standards for the design, inspection, and operation of LNG railcars and handling facilities. Other countries have similar regulatory requirements to ensure safety during LNG transloading.
4. Benefits of LNG Railcar Transloading
- Access to Remote Markets: Transloading to railcars allows LNG to be transported to areas without LNG pipelines, especially important for reaching remote industrial centers or underserved regions.
- Increased Flexibility: Rail transport allows for greater routing flexibility and can often avoid congested pipelines or ports, providing alternative delivery options and enhancing the LNG supply chain’s resilience.
- Economies of Scale: Moving LNG in large volumes by rail can be more cost-effective than truck transport over long distances, reducing logistics costs for LNG producers and end-users.
- Supply Chain Redundancy: The ability to transport LNG by rail provides a backup method when pipelines are at capacity, under maintenance, or facing regulatory restrictions.
5. Challenges in LNG Transloading to Railcars
- Infrastructure Costs: Setting up transloading terminals and railcars with specialized cryogenic equipment requires significant capital investment, making it viable primarily for regions with high LNG demand.
- Boil-Off Gas Management: Managing BOG is critical during long-distance rail transport. Prolonged travel times can lead to pressure build-up in the railcars, requiring efficient venting and insulation to keep the LNG in a liquid state.
- Safety Concerns: Handling cryogenic substances is inherently risky. Comprehensive safety protocols, training, and equipment are essential to prevent and manage potential incidents.
- Regulatory Challenges: Regulatory approval for LNG rail transport can vary by region, as not all countries allow LNG to be transported by rail due to safety and environmental concerns.
Summary
Transloading LNG to railcars is a valuable option for transporting LNG to areas without pipeline access or in cases where rail provides a cost-effective alternative. It requires specialized equipment, stringent safety measures, and compliance with regulatory standards. As demand for LNG continues to grow, especially in remote or underserved regions, transloading to railcars offers a practical solution for efficient, large-volume LNG transport. However, due to its high costs and safety challenges, LNG transloading infrastructure must be carefully planned and managed to optimize both safety and economic returns.
s.